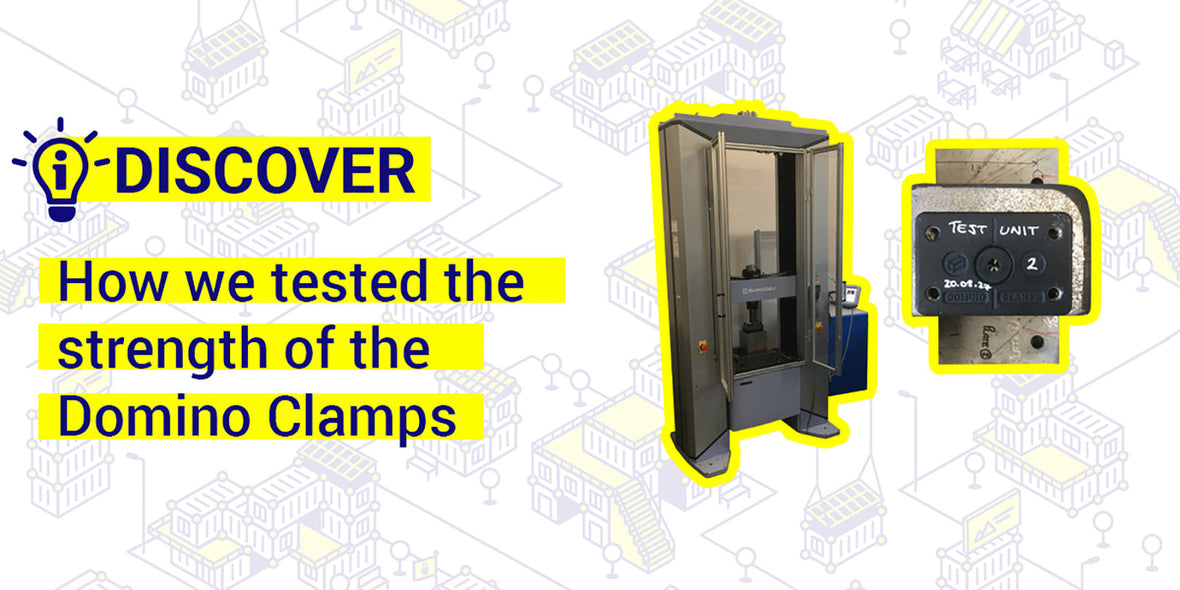
How we tested the strength of the Domino Clamps
As part of the design process for the Domino Clamp there were many considerations to make. We had to think about fabrication methods, materials and tolerances, and we spent over two years exploring these before finalising a design. However, there was always one area which we knew was going to be paramount to producing a safe and functional product…Testing and ensuring the strength and load taking capabilities.
We needed to ensure that along with everyday accessories like floodlights, CCTV and signage, that Domino Clamps would have the capabilities to support heavier attachments such as walkways, truss and roofing to fulfill the needs of customers like Eyal.
Testing Process
We initially decided on an allowable working load that we wanted to aim for that balanced out cost with usability. We got to this by working backwards from what would be needed for some of the more demanding applications we hoped Domino Clamps could be used for, and by speaking to project managers and riggers with experience in shipping container construction. With these figures in mind, we followed a 3-step process to test the Domino Clamp and modify the design accordingly. The first was to estimate a strength based on approximate hand calculations. Although these results are very rough and err on the side of caution, they allowed us to estimate the thickness of the plates which we could include in our 3D data model. Based on these results we moved one step closer to finalising the details of the design, which was drawn up into a provisional 3D drawing.
Once we had a 3D data model it was time to get more detailed in our estimations by getting the clamp analysed with a Finite Element model. A finite element analysis creates a simulation of a physical element by breaking it down into a mesh of smaller elements, and then using a complex numerical mathematical technique predicts the interaction between these smaller parts which combined provide a final result for the entire structure. This process is at the core of the majority of all engineering simulation software, from designing the fuselage of a plane to a multi-storey car park.
By getting our clamp analysed with this technique we were able to get a much more accurate, albeit still conservative, estimate of the Domino Clamp’s strength, which happily far exceeded our initial hopes. At this point we could move our prototyping into production and on to the final stage of the testing process.
The final and most important stage of testing is the physical testing. After researching various centers we opted for a UKAS accredited testing center based in the UK who became our partners in designing and executing the tests needed to be sure of Domino Clamps’ strength under different load conditions.
In order to get valid results we had to mimic the real life loading scenarios of the clamp in use, which meant building bespoke jigs using ISO corner castings from an ISO shipping container that could be placed under the specialist machinery. Once these were built and set up we could apply the load through the machine onto the Domino Clamp for each separate load case. The applied loads were extrapolated from the results of our FEA model and multiplied by two separate safety factors. Using dozens of our first batch of clamps, we conducted numerous tests under the various conditions and the reactions to each load were logged and assessed.
Results
With the testing logs and an adequate safety factor we pored over the results and were able to confirm the theoretical results provided by the FEA and provide the end user with a normal working load (NWL) for each direction of force. These have been summarised in our Technical sheet, together with all the relevant information needed for our customers to assess if our clamp is fit for their needs.
For more ingenious container solutions, useful information and offers delivered direct to your inbox, sign up to our information email 📨 or subscribe to our YouTube channel 📺