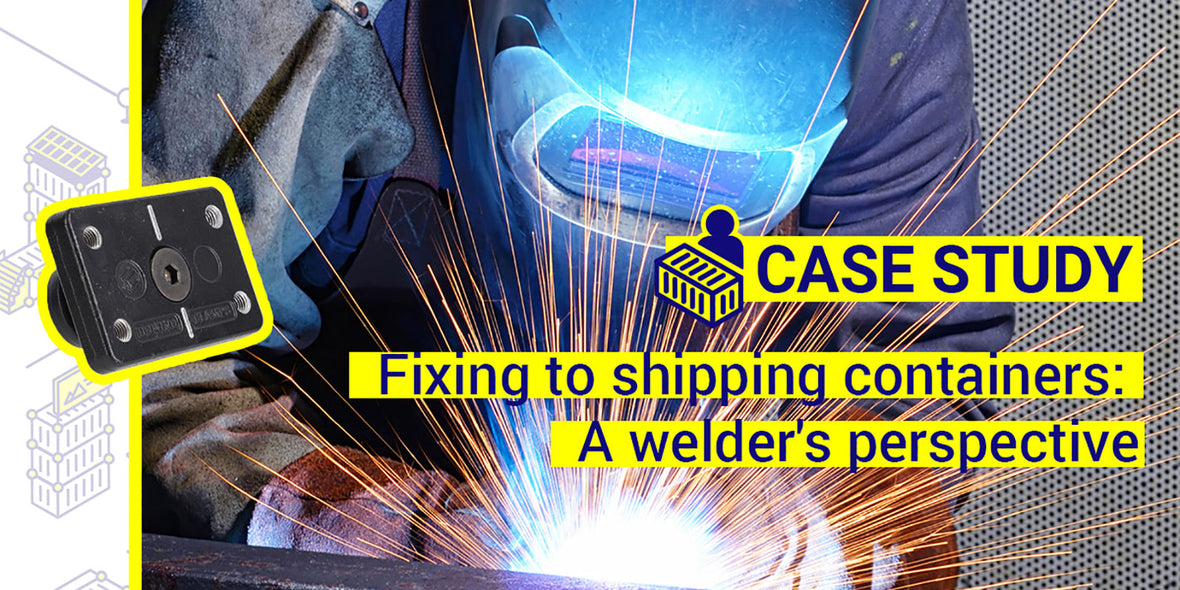
Fixing to shipping containers: A welder's perspective
In this blog we will be looking at the Pros and Cons of welding shipping containers compared to using a mechanical fixing like Domino Clamps. We spoke to Eyal Edelman, an experienced welder whose projects involving shipping containers include the Pop Brixton project in 2015.
What are your views on welding a shipping container as opposed to using mechanical fixings?
Although I am a metalworker, and primarily a welder, I would prefer to use off the shelf rated mechanical fixings as it removes the concern that there could be something amiss with the welding... It’s simply a question of eliminating doubt and reducing risk.
In what situation could a freelance welder find themselves culpable for a bad weld or if there was an issue with the welding?
It's not necessarily that you would find yourself culpable for a bad weld, it's more a case of reducing the overall risk in this situation. For example- If I was attaching a staircase or balustrade, I would rather use mechanical fixings as I know what the load capabilities would be rather than relying on the welding or having to go and get re-coded/re-ticketed.
Can you explain what being a coded/ticketed welder means?
Certain welding operations require a welder to be coded/ticketed. A coded or ticketed welder would have to reapply for the required ticket for a specific job to be carried out if required as this certification only lasts for 6 months. Not all welders will have this consistently unless they are working on projects that require it and because it is an expensive process they don't tend to get ticketed “just in case”.
Welder coding certificates must be signed every 6 months by a suitably qualified person to confirm the welder is still producing welds of the required standard and are formally re-tested at least every two years.
Is it always necessary for the welder working on the project to be coded/ticketed?
It’s not always necessary, no, but it can be a requirement where it is specified for the project. On some construction projects you will have a welding protocol that is passed from the designer or engineer to the welder. It will show not only what needs to be connected but the exact way the weld should work; specifying the weld pattern, bead size and so on.
Are there protocols that need to be followed for welding shipping containers?
For their manufacture, it is down to the manufacturer to ensure they are constructed following the ISO standards. However, for the modification or attachment to shipping containers it depends on the situation. It will be up to the Construction Site Manager or CDM as to whether everyone involved on the project needs to be coded or not. There are certain tiers of projects that necessitate this level of observation and management. Ultimately, someone in the chain needs to have taken responsibility for whichever method that was chosen and used.
What are the considerations when you have a shipping container on site that you want to modify?
Really someone needs to weigh up the risk involved, factoring in the kind of modifications, timeframe of its use, public exposure to it and any risks that might be involved, and make a decision based on that. If the modification or adjustment to the shipping container is done for the purpose of supporting the next phase of the project for public or personal use then you need to be looking potentially at something a bit more established as in getting it coded or someone to sign it off. There's no right or wrong answer necessarily, but someone needs to decide and take responsibility for the decision.
And if it is a commercial project?
Generally, if it is going to be used by the public afterwards like at Pop Brixton, it would need to be coded and signed off. These requirements are usually specified in the design, the welding could either be carried out by a coded welder or it can be carried out by a welder and then signed off by a structural engineer afterwards.
In the case of Pop Brixton, most of the modification work I was involved with was non structural, so the architects signed to assume responsibility. However the big bi-folding doors on the event space were structural, attached between two sections of containers stacked three high, so I ensured that a ticketed welder completed this particular task.
Could Domino Clamps have helped on this project?
Absolutely, Domino Clamps would have been useful here, allowing the hinges to be attached to the containers so it was a mechanical fixing as opposed to welding, this would have alleviated the need for a coded/ticketed welder and reduced the installation time substantially.
How difficult is it to weld attachments to shipping containers, considering the variation in thickness of the materials involved?
Welding thinner stuff to thicker materials shouldn't be an issue for an experienced welder, you just need to spend more time with the heat on the thicker material and then slowly move to the thinner material. However, corten steel needs to be welded with corten specific equipment for the Container Safety Convention (csc) certificate to remain valid, so this is a consideration if the container is going to be reused for shipping purposes at a later date. You also need to clean the weld up and prime and paint it afterwards, to prevent rusting.
So what are the advantages of welding a shipping container in your opinion?
Welding is really fast, you don't need to spend time cutting holes, aligning those holes etc. It's quick and easy if you have access and the skills to use the equipment, just weld and go. So welding is ideal for a structure that will not be moved or accessories that will not need removing.
And the disadvantages?
It is difficult to remove the welds if you want to remove the attachments, it's unlikely that the shipping containers would be reusable at sea afterwards. And again, the cut off welds need to be cleaned, primed and painted… again.
Although you can weld anywhere on the shipping container most areas apart from the corners and the horizontal and vertical sections are not really strong enough to hold attachments without reinforcement.
Welding is a hot process, so in regards to HSE the job needs to be risk assessed and protective equipment used.
Finally, you are relying on the weld’s integrity to remain intact, and as we’ve spoken about, someone needs to take responsibility for that.
And what are the advantages of using mechanical fixings such as Domino Clamps?
If you go to the shop and buy mechanical fixings you can look up all the properties; you know the load and shear; you can calculate how many you need, if you need to up or downscale. There ought to be minimal to no risk using mechanical fittings when used correctly.
Similarly, Domino Clamps have been tested so you know what their ratings are from the start. Making it easier for the designers or architects. Their job is also made easier at this stage because they can price things up accurately, as opposed to welding where you would be paying a day rate and have to estimate the number of days needed.
Like other mechanical fixings they are easily removed and can be reused for another project if required, but have the added bonus of not damaging the container.
You know exactly where they are going to be fitted, so it makes design decisions easier and reduces the time you need to be onsite in the elements, can be prefabricated and then taken to site.
Domino Clamps or other mechanical fixings are less specialised, you don't need specific training to use them. The person who installs a Domino Clamp is going to cost a lot less than a ticketed welder.
And the disadvantages?
Well, you can only attach something to the corner casting, although if you attached a Domino Clamps to both corners you can attach something between the two to provide fixing points if required. With welding, you can attach anything, anywhere which can be a big help. But as I mentioned, this comes with all the disadvantages we have spoken about already.
To discuss how Domino Clamps can help your project send us an email hello@dominoclamps.com
For more ingenious container solutions, useful information and offers delivered direct to your inbox, sign up to our information email 📨 or subscribe to our YouTube channel 📺