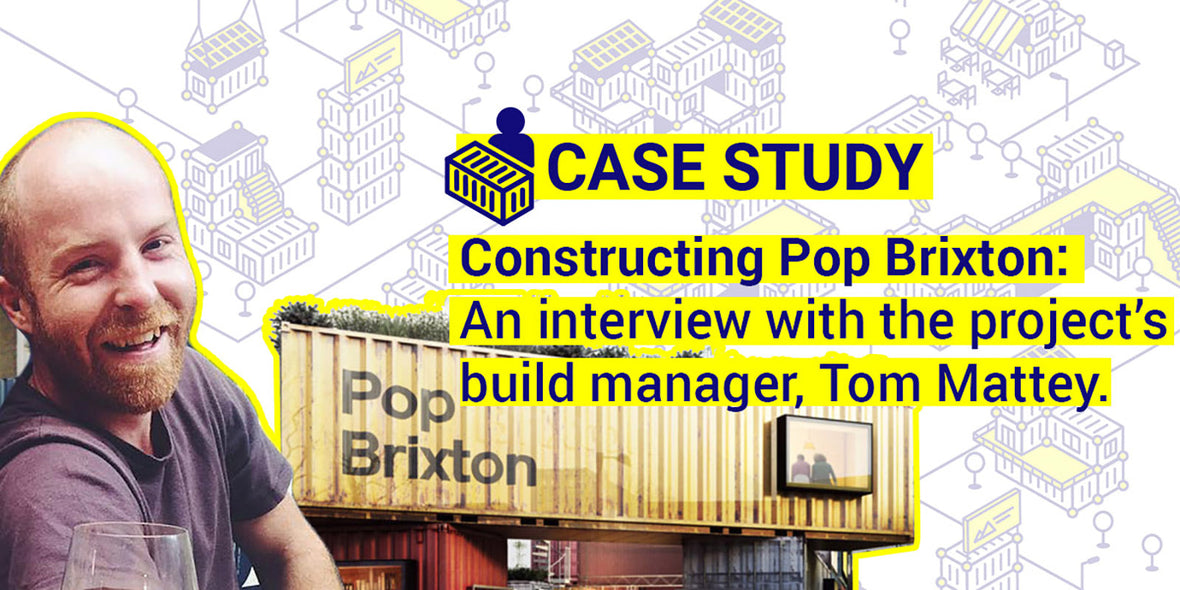
Constructing Pop Brixton: An interview with the project's build manager, Tom Mattey
Pop Brixton is a temporary project that has turned disused land into a creative space for 55 local independent businesses including restaurants, retailers, makers, street food traders, designers, digital start-ups, a community barbershop, a youth radio station and a number of social enterprises.
The project, using 57 recycled shipping containers and other reclaimed materials, was started as an incubator for start-ups to enable locals to test the market and get their businesses off the ground.
We spoke with Pop Brixton’s build manager, Tom Mattey about the project.
Can you introduce yourself and say a little about your involvement with the construction of Pop Brixton
I am a builder by trade, with experience across multiple trades, and specialising in working with shipping containers. I started working on Pop Brixton as a tradesman in 2015 and ended up being site manager, build manager, and park manager all rolled into one. I was working directly with the architects and Lambeth council who are partners on the project with Make Shift. After six months of construction, the project opened its doors on the 29th of May 2015.
Why were you hired in?
I was originally hired in to lay the foundations for the shipping containers and run the apprentice scheme with Lambeth College, but it quickly became clear that I was the right person to run the whole build project.
What did the Pop Brixton project involve?
The project was one of the most imaginative designs I have seen, using shipping containers and other reclaimed materials it incorporates cross stacking of the containers, lots of bridges, stairs and multiple supports.
What were the challenges you faced?
Although I specialised in working with shipping containers, I had not worked on a project of this scale before, with containers being stacked four storeys high in places.
My experience had previously been with more basic builds and conversions, involving three or four containers.
Construction wise, the intricate design meant there were constructability challenges posed between architectural diagrams and build application. There was four months’ worth of welding site wide, and one particular walkway literally took 1 week of welding to get everything together and stable.
And of course, managing a crew of up to 60, including 16 apprentices on a daily basis, was a challenge in itself.
Any surprises?
One day we arrived on site to find that a stack of three shipping containers had moved about 30cm along the ground. This was before the resin anchored foundations and fixings had been put in place. After a few hours of investigation, the only viable conclusion was that it had been extremely windy the night before and this had caused the movement.
Can you see ways in which Domino Clamps would have made construction easier?
Absolutely! Welding to containers can be tricky, the thicker steel takes longer to heat up so when you are attaching accessories that are half the thickness of the container it’s not ideal. And at £350 per day for a ticketed welder to be on site it was an expensive process to get the lighting, power, extraction and stretch tent mounted at the end of the project. That's without all the welding that took place during the actual construction phase to attach the walkways, stairs and bridges.
What could Domino Clamps have been used for?
During the build, even simple things like the poles of lighting and overhead cabling would have been ideal, along with other attachments such as handrails and stairs. And to get a subcontractor on site post build to fit something like the extraction units for the restaurants, would have been a much easier process. Just attaching a Unistrut frame to a Domino Clamp with a few hand tools as opposed to getting a welder to do it would have saved thousands of pounds.
Literally everything that needed to be attached to the shipping containers could have been done "quicker, cheaper and more easily using Domino Clamps".
What were your thoughts when you first saw and held a Domino Clamp?
It’s a lot heavier and sturdier than I imagined, I don't think you can appreciate how solid they are until you hold one in your hand. I would be extremely confident attaching stairways and other requirements up to the second level without the involvement of engineering. Obviously they have been tested extensively for recommended working loads but I would have to engage my engineers for additional advice above and beyond that level.
What difference would Domino Clamps have made to the deconstruction process?
This is a phone call I am not looking forward to receiving to be honest, but if Domino Clamps had been used on the project it would be a much quicker and easier process. There are thousands of welds that need to be cut, it's going to be a health and safety nightmare, if we had used Domino Clamps it would just be a case of unbolting the attachments and removing the Domino.
I imagine it will take almost as long to dismantle this project as it took to construct it, if not longer.
To discuss how Domino Clamps can help your project send us an email hello@dominoclamps.com
For more ingenious container solutions, useful information and offers delivered direct to your inbox, sign up to our information email 📨 or subscribe to our YouTube channel 📺